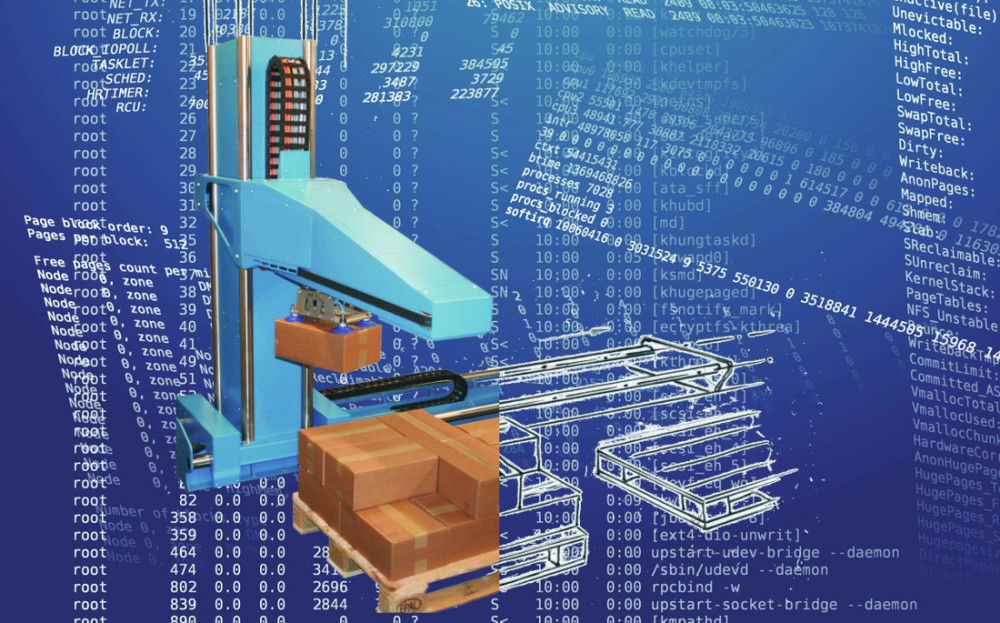
Nicht immer sind sechs-achsige Knickarmroboter die perfekte Wahl. Für Palettieraufgaben eignen sich vier-achsige Roboter besonders gut.
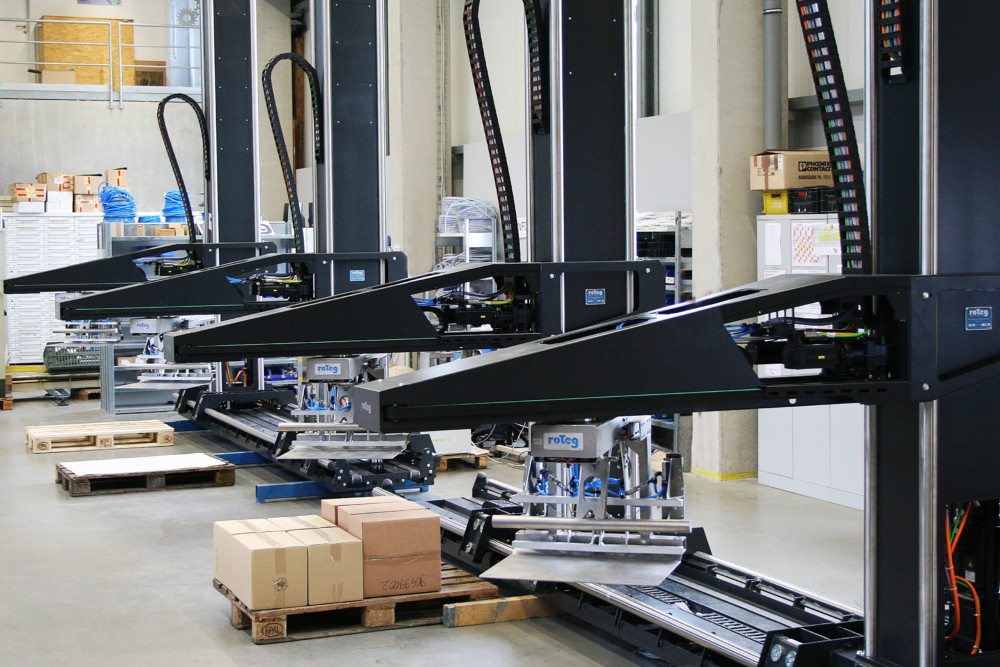
Beim Palettieren kommt es vor allem auf einen angepassten Greifraum, hohe Traglasten sowie eine robuste Technik an. Eine besonders hohe Positioniergenauigkeit ist hingegen weniger gefragt.
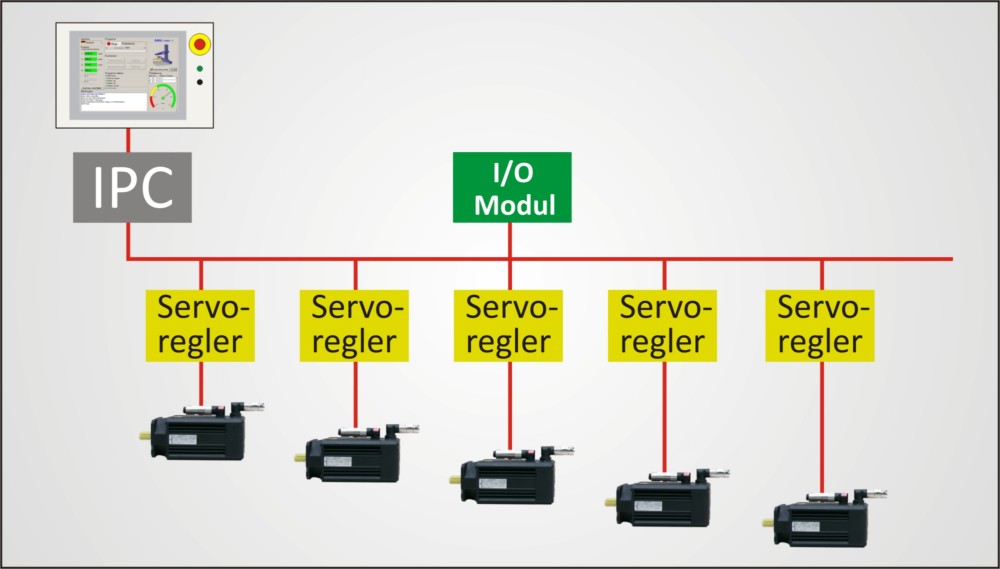
Durch den Einsatz des CAN-Bus-Systems konnte man riesige Kabelbäume auf ein Minimum reduzieren.
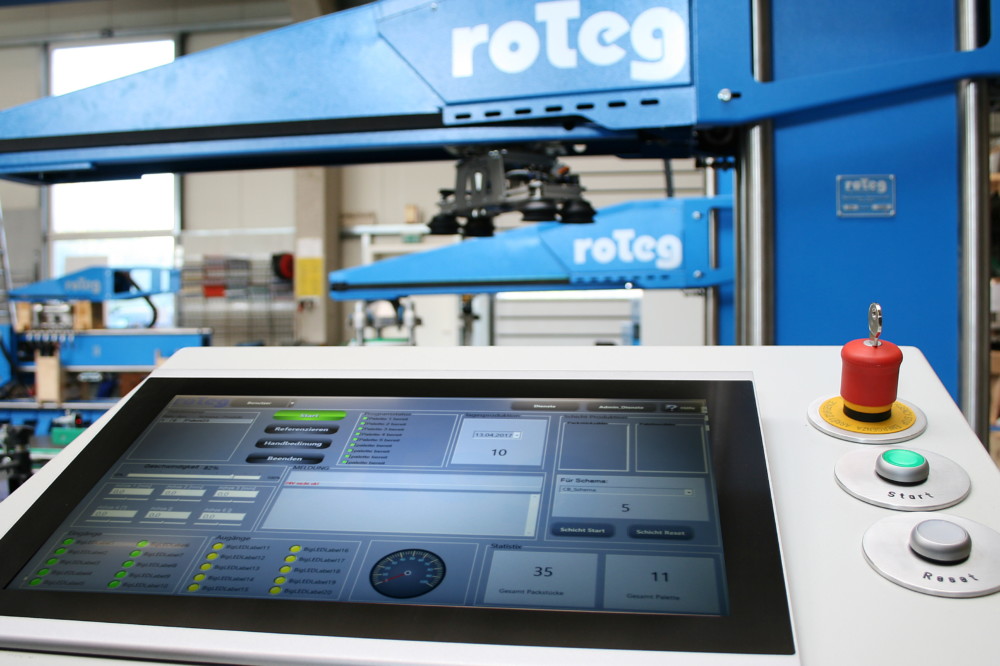
Eine bedienerfreundliche Steuerungssoftware ist besonders wichtig für Roboteranlagen. Dies wird jedoch oft vernachlässigt.
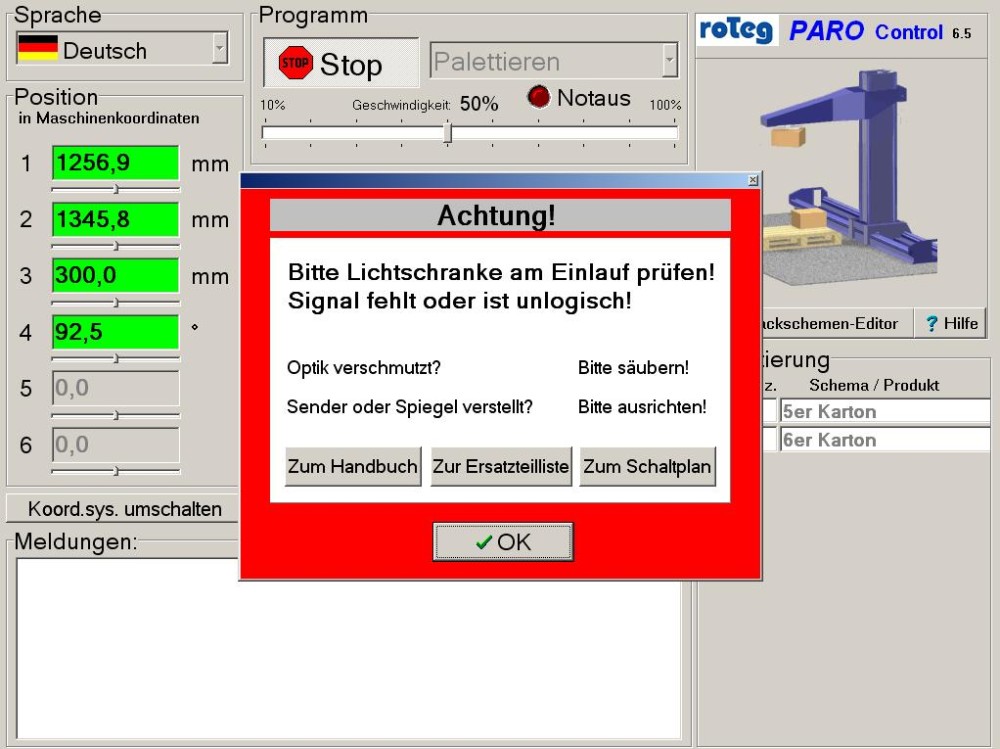
Besonders gute Systeme melden Fehler und schlagen direkt Lösungen vor.
Was ist ein Roboter?
Der Begriff Roboter weckt bei vielen immer noch die Vorstellung des stählernen Kollegen, der mit Armen und Beinen und beeindruckender Intelligenz fast beliebige Aufgaben übernehmen kann. In produzierenden Unternehmen nennt man die stählernen Mitarbeiter Industrieroboter. Sobald diese in Bezug auf Bauart oder System für spezielle Aufgaben ausgelegt sind, werden die Bezeichnungen konkreter – wie etwa Lackierroboter, Schweißroboter oder Palettierroboter.
Die Entwicklung des Marktes
Ursprünglich hatten alle Roboterentwickler im Auge, möglichst jede Handhabungsaufgabe durch den Einsatz eines Standard-Industrieroboters zu lösen. Lange war es das Ziel, immer schnellere Geräte mit verbesserter Positioniergenauigkeit zu bauen. Der Markt war geprägt durch sechs-achsige Knickarmroboter in mehreren Baugrößen und mit unterschiedlichen Traglastklassen. Die Konsequenz: Die Automation mit dieser Technik ist nicht immer optimal und oft besonders kostenintensiv. Deshalb ist es nicht verwunderlich, dass es mittlerweile einige Sonderbauformen gibt, die sich von der klassischen Standardbauweise deutlich unterscheiden.
Ein Beispiel sind die Palettierroboter. Beim Palettieren stehen Forderungen im Raum wie ein angepasster Greifraum für die Palettierung, hohe Traglasten sowie eine robuste Technik. Weniger gefragt ist hier eine hohe Positioniergenauigkeit. Dadurch stellt sich die Frage, ob und wie die konkurrierenden Systeme miteinander verglichen werden können und welche Unterscheidungskriterien für die zu lösende Handhabungsaufgabe wichtig sind. Bei näherer Betrachtung kristallisieren sich zwei wichtige Beurteilungskriterien heraus
- Gelenkigkeit und Greifraum (Bauform):
Ein Roboter muss handhabungstechnisch geprägte Aktionen im Raum realisieren, indem er ein Objekt wie z.B. ein Werkzeug oder ein Werkstück aufgrund der Gestaltung seiner kinematischen Bewegungsmöglichkeiten im Raum frei bewegen kann. - Steuerung und Intelligenz:
Der Roboter muss mittels einer programmierbaren Steuerung Bewegungsaktionen ausführen, die mathematisch logischen Abläufen folgen. In diesem Zusammenhang fällt immer wieder der Begriff des „Intelligenten Systems“.
Roboterbauarten, Greifraum und Freiheitsgrade
Betrachtet man den heutigen Markt der Industrieroboter, so fallen zuerst einmal die verschiedenen Bauarten (Kinematiken) auf. Prinzipiell bestehen alle Geräte aus einer sinnvollen Kombination von Drehgelenken und Linearführungen, die durch einzelne Antriebe unabhängig bewegt werden können. Der Fachmann spricht hier von den Bewegungsachsen und von der Gestaltung der kinematischen Kette.
Wie viele Achsen braucht ein Roboter?
Um dies zu beantworten ist ein kleiner Ausflug in die Mathematik hilfreich. Wenn der Mathematiker ein Objekt im Raum beschreibt, so nutzt er sechs Freiheitgrade. Die ersten drei dienen zur Beschreibung der grundsätzlichen Position im Raum. Im kartesischen Koordinatensystem wird diese Position mit den Variablen X, Y und Z beschrieben. Im Roboterbereich sind die ersten drei Achsen ebenfalls für den Arbeitsraum verantwortlich und somit für die grobe Position des Aktionspunktes im Raum. Auch, wenn dieser Zusammenhang durch die gegenseitige Beeinflussung aller Gelenke Rückwirkungen auf alle Achsstellungen haben kann, sind diese ersten drei Achsen doch für die grundsätzliche Größe des Greifraumes verantwortlich und werden deshalb auch als Hauptachsen bezeichnet. Die jeweilige Kombination der Dreh- und Linearachsen bestimmt den nutzbaren Greifraum. So führen Geräte, die ausschließlich aus Drehachsen bestehen, systembedingt zu einem kugelig geprägten Greifraum. Geräte mit Linearachsen weisen prinzipiell kubische Greifräume auf.
Palettieren mit vier Achsen
Sofern das im mathematischen Raum befindliche Objekt auch gedreht und/oder geschwenkt werden muss, führt der Mathematiker drei weitere Freiheitgrade ein und hat damit nun auch die mathematisch Kontrolle über Position und Orientierung seines Objektes. In der Robotik sind analog dazu drei weitere Achsen notwendig, um dem Gerät die Gelenkigkeit zu verleihen, Objekte im Raum beliebig zu orientieren. Es handelt sich hierbei um die Handachsen des Gerätes.
Die volle Gelenkigkeit in allen sechs Achsen ist in einigen Fällen aber gar nicht notwendig. Für übliche Palettiervorgänge sind beispielsweise all die Achsen überflüssig, die ein Schwenken der Packstücke zur Folge haben. Alleinig die Drehung um die Senkrechte ist hier sinnvoll. Mit dem typischen vierachsigen Palettierroboter können auf allen üblichen Ladungsträgern beliebige Palettiermuster erzeugt werden.
Steuerung und Intelligenz
Wenn der zuvor beschriebenen Mechanik die „Intelligenz“ fehlt, so nutzt die schönste Optik eines Roboters nichts. Dem Steuerungssystem mit dem zugehörigen Bedienkonzept und Programmierverfahren schenkt man oft zu wenig Aufmerksamkeit. Für viele Anwendungen ist dies jedoch der wahre Schlüssel zum Erfolg.
Elektrik, Verdrahtung, Steuerungshardware
Voraussetzung zur Programmierung des Systems „Roboter“ ist erst einmal, dass die Steuerung die volle Kontrolle über alle Achsantriebe besitzt und die notwendigen Informationen über die Gelenk- bzw. Achsstellungen und die Zustände der Ein- und Ausgänge der gesamten Roboterzelle steuerungstechnisch unter Kontrolle hat. Betrachtet man in diesem Zusammenhang die zu verdrahtenden Komponenten wie Antriebsmotoren, Positionssensoren, digitale und analoge Eingänge sowie die notwendigen Ausgänge, ergeben sich zwangsläufig dicke Kabelbäume. Diese müssen zudem über mehrere Gelenke und Führungen hinweg permanent bewegt werden. Aus diesem Grund waren vor wenigen Jahren Kabelbrüche noch an der Tagesordnung und führten nicht selten zu zeitaufwändigen Reparaturen.
Aber auch hier haben sich in den letzten Jahren technisch sehr interessante Lösungen ergeben. Zu nennen sind hier vor allem die Bus-Systeme. Hierbei überträgt ein hochflexibles Kabel alle Informationen in beide Richtungen. Der Kabelbaum ist mit dieser Technik auf zwei Leitungen geschrumpft. Über die eine Leitung wird die Energie übertragen, über die andere Leitung alle notwendigen Information.
Der PC als Maschinensteuerung
Als Steuerungsbasis greift man heute immer häufiger auf den PC zurück. Industrie PCs laufen unter den modernen Betriebssystemen stabil und zuverlässig. Auch ist es kein Problem mehr, die Steuerungsprogramme mit Echtzeitfunktionalitäten auszustatten. Genau dieser Punkt hatte lange die Nutzung der Ps als Steuerungssysteme behindert.
Da der Umgang mit Maus und Tastatur für den Industriebereich nicht sehr komfortabel ist, hat sich hier der Touchscreen als Alternative etabliert. Er erlaubt eine einfache Kommunikation mit dem System per Fingerdruck. Die Maschinenbedienung über den Touchmonitor hat sich zwischenzeitlich nicht nur im Roboterbereich bewährt und stellt eine komfortable Möglichkeit der Gestaltung der Bedienerkommunikation dar. Schon 1999 lieferte die Firma roTeg die ersten Roboter mit einer PC-Steuerung und Touch-Bedienoberfläche aus. Die Steuerungssoftware wird bei diesen Systemen ähnlich wie zum Beispiel die bekannten Office-Anwendungen installiert und gestartet. Die gesamte Kommunikation zur Roboterhardware läuft danach über ein Bus-System, so dass es sich bei dem Steuerungs-PC um ein handelsübliches Gerät ohne spezielle Modifikationen handelt.
Die Programmierung
Und hier wird es jetzt so richtig wichtig.
Schaut man sich die Handbücher der unterschiedlichen Roboteranbieter auf dem Markt an, so fallen sofort Parallelen zu den Programmiersprachen Basic, Pascal oder C auf. Diese Hochsprachen aus der Computerwelt eignen sich hervorragend, um einem Roboter zu sagen, was er zu tun hat. Alle Handhabungsaufgaben, die sich logisch und mathematisch beschreiben lassen und zu dessen Ablauf die notwendigen sensorischen Informationen vorliegen, können so in einen Programmablauf überführt werden. Die Möglichkeiten sind fast unerschöpflich. Noch heute sind laufend interessante Anwenderberichte über neue Roboterlösungen in den Fachzeitschriften zu finden.
Anwenderfreundlichkeit bleibt auf der Strecke
Doch hier liegt auch das große Problem der Roboterapplikationen. Ein mächtiges Werkzeug braucht auch hervorragende Programmierer, um alle Möglichkeiten der Systeme in vollem Umfang ausschöpfen zu können. Hier ist der Vergleich mit einer Fremdsprache durchaus zulässig. Eine Sprache zu beherrschen kann heißen, sich leidlich zu verständigen. Es kann aber auch bedeuten, dass man Romane und Gedichte schreiben kann. Auch, wenn der handhabungstechnische Ablauf geschickt programmiert ist und alle Abläufe optimal verknüpft sind, bedeutet das noch lange nicht, dass der spätere Bediener mit der Anlage problemlos und komfortabel arbeiten kann.
Hier zeigt sich ein weiteres Kriterium zur Beurteilung der Qualität eines Robotersystems. Denn ein anwenderfreundliches Bedienkonzept bleibt oft trotz eines guten Programms auf der Strecke. Was ist bei einer Störung oder einem kleinen Fehler? Wie schnell ist solch ein Fehler behoben und welche Qualifikation muss ein Bediener mit sich bringen, um den Fehler zu lokalisieren und zu beheben? Gute Systeme zeichnen sich in diesem Punkt durch einen anwenderfreundlichen Dialog aus. So ist es heute durchaus möglich, dass der Roboter – oder besser die Steuerung – viele Fehler selbst erkennt, lokalisiert und Lösungsvorschläge unterbreitet.
Beispiel Kabelbruch
Einen Kabelbruch am Resolver eines Motors können heute fast alle Regler selber erkennen. Gute Systeme reichen solche Fehler in verständlicher Form an den Bediener weiter. Sinnvoll ist es hierbei, dass die Steuerung sofort einen Lösungsvorschlag unterbreitet und dem Bediener in Bild und Text sagt, was er zur Fehlerbehebung unternehmen muss. Heute vor allem wichtig sind Fehlermeldungen zu defekten Lichtschranken.
Lösungsvorschläge vom Roboter
Bei Anwahl „zum Handbuch“ oder „zum Schaltplan“ erfolgt ein Sprung zu den auf der Steuerung hinterlegten Dokumenten. Diese kleinen und sehr hilfreichen Programmierlösungen müssen nicht immer neu programmiert werden. So sind heute im Bereich der Palettierroboterzellen die meisten kleinen Probleme bekannt und die möglichen Hilfen für die Problembehebung bereits programmiert. Daher gibt es viele kleine und große Hilfestellungen, die eine gute Software für Palettieranwendungen bereits standardmäßig beinhalten sollte.
Ebenfalls ist es heute Standard, dass der Anwender die Palettiermuster selber programmieren kann. Bei komfortablen Systemen können sich heutige Steuerungen nach Eingabe der Abmessungen des Packstücks die Palettiermuster selber errechnen oder auf Wunsch dem Bediener Vorschläge zu möglichen Palettiermustern unterbreiten. Das gewünschte Lagenbild und die Lagenanzahl kann so ausgewählt werden und der Palettiervorgang kann sofort starten.
So ist je nach Anwendungsfall und Aufgabenstellung immer zu prüfen, welches der am Markt befindlichen Systeme sich für die jeweilige aktuelle Aufgabe besonders gut eignet. Hierbei ist nicht nur die reine Mechanik zu betrachten, sondern auch das dahintersteckende Steuerungs- und Bedienkonzept. Dieses stellt gerade im Roboterbereich ein wichtiges Kriterium zur Systemauswahl dar.